Baseball caps are more than just fashion statements—they blend style, function, and craftsmanship in ways many people never consider. From trendy streetwear to sports arenas, these iconic hats protect, express identity, and unite communities worldwide. But how exactly are baseball caps made? Understanding the process reveals a fascinating journey involving material selection, design precision, skilled stitching, and quality control.
In brief, baseball caps are made by selecting suitable fabrics, cutting patterns precisely, stitching panels together, attaching visors and closures, and undergoing rigorous quality checks to ensure durability and comfort. This multi-step process combines technology and craftsmanship to produce high-quality, stylish caps.
Imagine the story behind your favorite cap—from raw materials in sustainable factories to hands of skilled workers and finally onto your head. This detailed guide will take you through every step, uncovering secrets and innovations in baseball cap manufacturing. Let’s dive deeper.
1. What materials are used to make baseball caps?
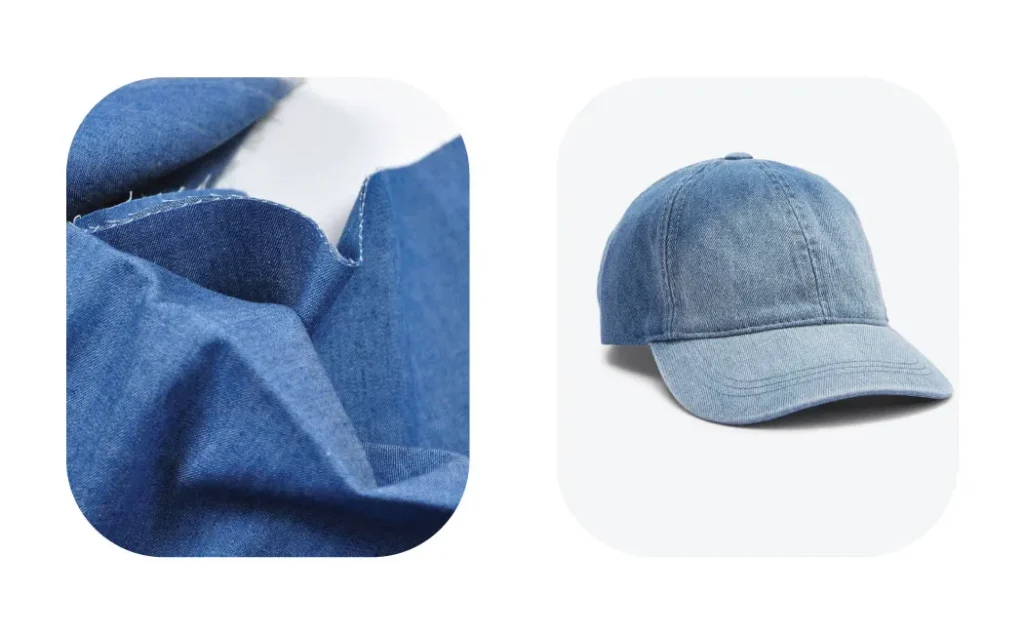
Baseball caps are typically made from cotton, polyester, wool blends, or eco-friendly fabrics like recycled polyester. The choice of materials affects breathability, durability, and sustainability.
Materials include cotton for softness, polyester for durability, wool for warmth, and recycled fabrics for eco-friendly options. Accessories like plastic or metal closures and inner sweatbands complete the build.
- Cotton vs. Polyester: Cotton caps offer comfort and breathability, ideal for casual wear. Polyester is stronger and moisture-wicking, favored in sports caps. Some blends combine the best of both.
- Sustainability in Fabrics: Growing demand for sustainable fashion pushes manufacturers to adopt recycled polyester and organic cotton. These reduce environmental footprints but may impact cost and texture.
- Sweatbands and Linings: Usually made from cotton terry or moisture-wicking materials, sweatbands improve comfort by absorbing sweat and preventing slippage.
- Closures and Visor Materials: Plastic snapbacks, metal buckles, or Velcro straps each bring different durability and adjustability profiles. Visors use stiffened fabrics or plastic inserts to maintain shape.
- Innovation Spotlight: Some brands experiment with biodegradable fabrics or bamboo fibers, aligning with eco-conscious consumers.
By examining material properties and their trade-offs, manufacturers balance cost, performance, and environmental impact to meet diverse consumer needs.
Material Type | Characteristics | Typical Use | Sustainability Aspect |
---|---|---|---|
Cotton | Soft, breathable | Casual wear, sweatbands | Organic cotton available |
Polyester | Durable, moisture-wicking | Sports caps, performance wear | Recycled polyester options |
Wool Blends | Warm, classic look | Winter caps | Less common eco options |
Recycled Fabrics | Eco-friendly, variable feel | Sustainable fashion lines | Reduces waste & carbon footprint |
Closures (Plastic/Metal) | Adjustable, durable | Snapbacks, strapbacks | Some recyclable plastics |
Visor Inserts | Shape retention | Brim stiffness | Plastic or cardboard inserts |
2. Which machines and tools are involved in baseball cap production?
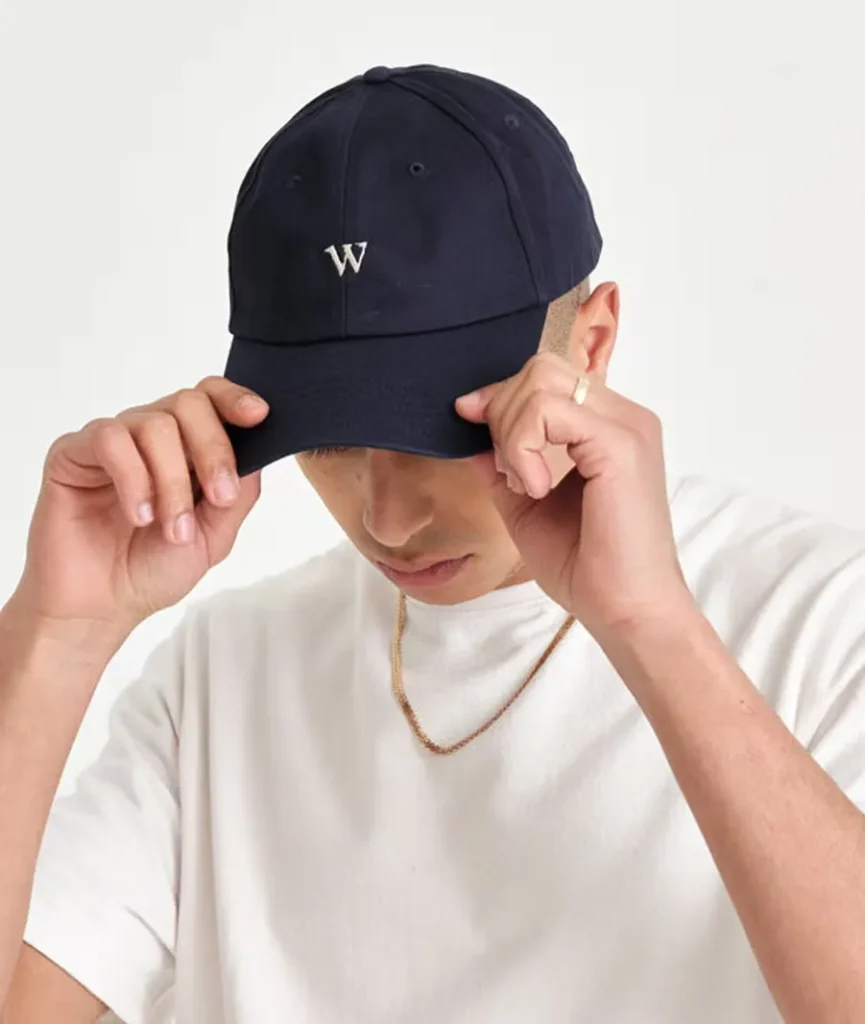
Modern baseball cap manufacturing uses cutting machines, sewing machines, embroidery machines, and finishing tools to ensure efficiency and consistent quality.
Production relies on automated cutters for precision, industrial sewing machines for durable stitching, and embroidery machines for logos, all crucial to high-quality cap making.
- Cutting Machines: Computerized fabric cutters slice materials with millimeter accuracy, minimizing waste. Laser cutters provide clean edges and faster turnaround.
- Sewing Machines: Lockstitch and overlock machines handle seams, providing strength and flexibility. Multi-needle machines enable rapid stitching of complex patterns.
- Embroidery Machines: Automated embroidery machines stitch logos and designs with high precision. Customization options are vast, from thread colors to complex patterns.
- Heat Press and Labeling Equipment: Heat presses apply patches and labels. Label machines add branding and care tags efficiently.
- Automation vs. Handcraft: While machines speed up production, skilled workers still perform quality checks and intricate finishing touches.
The integration of these machines enables manufacturers to produce thousands of caps per day without sacrificing quality, meeting high demand globally.
Machine/Tool | Function | Benefits | Notes |
---|---|---|---|
Computerized Cutters | Precise fabric cutting | Reduces waste, speeds process | Laser cutters for clean cuts |
Lockstitch Sewing | Strong seam stitching | Durable seams | Most common stitch type |
Overlock Sewing | Finishes seam edges | Prevents fraying | Provides neat interior finish |
Embroidery Machines | Logo and design stitching | High precision customization | Multi-needle, programmable |
Heat Press | Applies patches/labels | Fast branding application | Common for team logos |
Labeling Machines | Attach care and brand labels | Efficient, consistent labeling | Quality control aid |
3. How is the baseball cap pattern designed and cut?
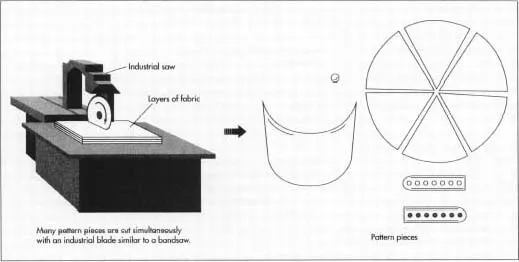
Patterns for baseball caps are created based on specific style templates and head sizes, then cut with precision to ensure perfect panel shapes and fit.
Cap patterns are designed digitally or manually, then cut using automated cutters to ensure accuracy and reduce fabric waste.
- Digital Pattern Design: CAD software allows designers to create exact panel shapes, accounting for seams, darts, and crown height.
- Style Variations: Different cap styles (6-panel, 5-panel, dad hats) require unique patterns, impacting fit and aesthetics.
- Prototyping: Patterns are first tested on muslin or cheaper fabrics to adjust sizing and shape before mass production.
- Cutting Precision: Automated cutters follow digital patterns to minimize errors, ensuring all parts align perfectly during assembly.
- Waste Reduction: Efficient nesting algorithms optimize fabric layout, reducing scraps and costs.
Pattern design is foundational—any mistake here can lead to poor fit or defects, so it demands meticulous attention.
Aspect | Description | Importance | Example |
---|---|---|---|
Digital Design | Use of CAD software | Precision, easy edits | Adjust crown height digitally |
Style Variations | Number and shape of panels | Affects fit and look | 6-panel vs. 5-panel caps |
Prototyping | Sample testing with cheaper fabric | Validates fit and shape | Muslin mock-ups |
Cutting Accuracy | Automated cutters follow patterns | Minimizes errors and waste | Laser cutting |
Nesting Algorithms | Optimize fabric layout | Reduces fabric scraps | Maximizes material use |
4. Do baseball caps require special stitching techniques?
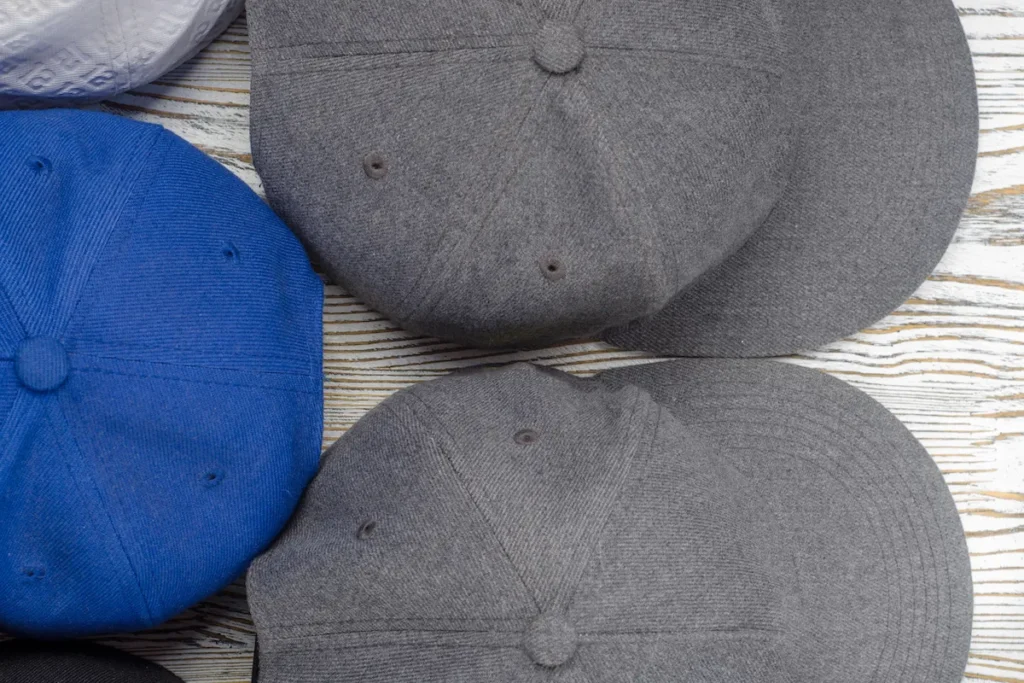
Yes. Specialized stitches like lockstitch and overlock are used to assemble panels, attach visors, and reinforce stress points, ensuring strength and neatness.
Stitching uses lockstitch for durability and overlock for seam finishing, critical for maintaining cap shape and longevity.
- Lockstitch: The most common stitch type, providing a strong seam that resists unraveling. Essential for joining cap panels.
- Overlock (Serger): Finishes raw fabric edges, preventing fraying and giving a clean interior finish.
- Topstitching: Often visible on visors and crowns, it adds decorative appeal and structural support.
- Bar Tacking: Reinforces high-stress areas like visor edges and sweatbands to prevent tearing.
- Thread Quality: Polyester or nylon threads are preferred for strength and colorfastness.
The choice of stitching impacts not only durability but also the final look and comfort of the cap.
Stitch Type | Purpose | Application | Key Benefit |
---|---|---|---|
Lockstitch | Primary seam stitching | Joining fabric panels | Durable, resists unraveling |
Overlock (Serger) | Seam finishing | Inside seam edges | Prevents fraying |
Topstitching | Decorative and structural | Visor edges, crown panels | Adds strength and style |
Bar Tacking | Reinforcement | High-stress points | Prevents seam tearing |
Thread Type | Polyester/Nylon preferred | All stitching | Strong, colorfast |
5. How is the cap assembled and shaped?
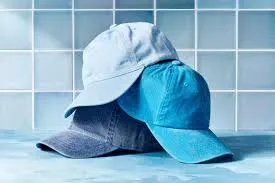
Assembly involves sewing the fabric panels together, attaching the visor, inserting the closure, and shaping the crown to fit heads comfortably.
Caps are assembled by stitching panels, attaching visors and closures, then shaped using pressing machines or hand molding to achieve the iconic silhouette.
- Panel Assembly: Sewn together carefully to maintain symmetry and prevent puckering.
- Visor Attachment: The visor is stitched and often reinforced with plastic or cardboard inserts for stiffness.
- Closure Installation: Adjustable straps or fitted bands are attached, allowing for a customizable fit.
- Crown Shaping: Steam pressing or molding machines shape the crown. Some hats include internal supports to hold shape.
- Finishing Touches: Sweatbands, labels, and eyelets (for ventilation) are added last.
This stage requires a blend of machinery and skilled labor to produce caps that look great and feel comfortable.
Step | Description | Tools/Methods | Importance |
---|---|---|---|
Panel Sewing | Join cut fabric panels | Industrial sewing machines | Maintains shape & fit |
Visor Attachment | Attach and reinforce visor | Stitching, plastic inserts | Provides brim stiffness |
Closure Installation | Add adjustable strap or band | Sewing, snaps, buckles | Customizable fit |
Crown Shaping | Form cap shape | Steam press, molding tools | Achieves iconic silhouette |
Final Touches | Add sweatbands, labels, eyelets | Manual & machine processes | Comfort, branding, ventilation |
6. Are there quality control and finishing processes in baseball cap manufacturing?
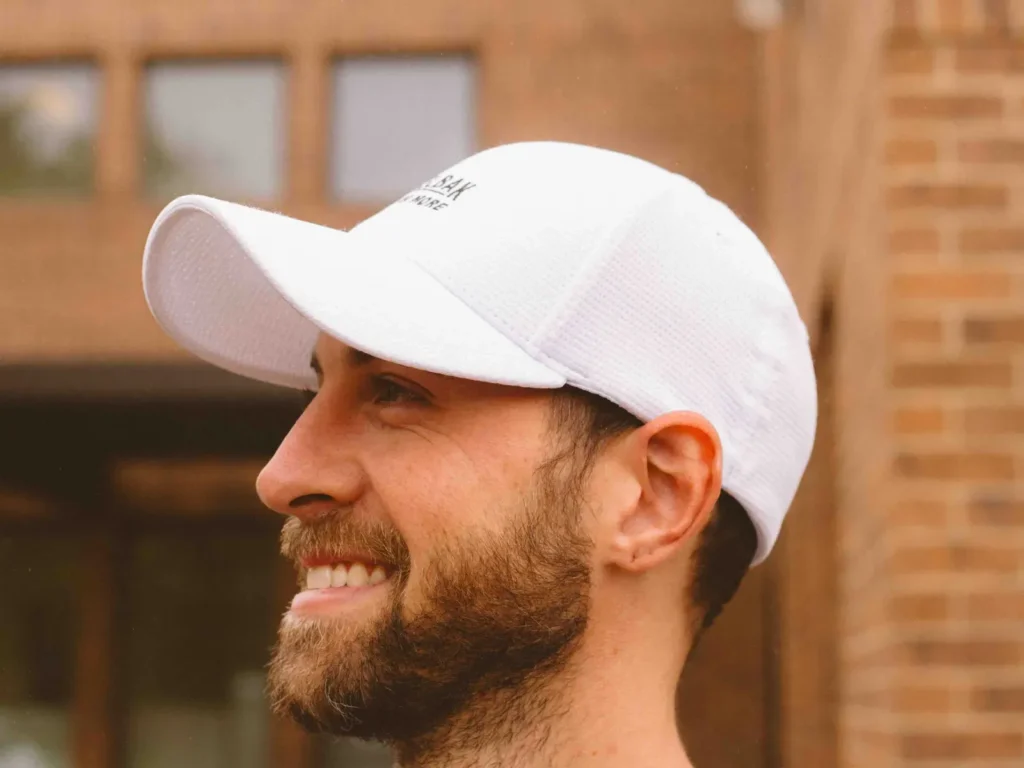
Yes. Caps undergo rigorous inspections for stitching integrity, fabric defects, fit, and overall appearance before packaging.
Quality control includes visual inspection, fit testing, seam strength tests, and packaging to ensure caps meet standards and customer expectations.
- Visual Inspection: Checks for fabric flaws, color consistency, and stitching defects.
- Seam Strength Testing: Measures how much force seams can withstand before breaking.
- Fit Testing: Ensures sizing accuracy and comfort.
- Packaging: Caps are folded or stuffed with tissue paper to maintain shape, labeled, and boxed for shipping.
- Sustainability Considerations: Some manufacturers use recyclable packaging and minimal plastic to align with eco-friendly goals.
Comprehensive QC ensures that only caps passing strict criteria reach customers, protecting brand reputation.
QC Aspect | Description | Method | Impact |
---|---|---|---|
Visual Inspection | Check fabric, color, stitching | Manual inspection | Ensures aesthetic quality |
Seam Strength Test | Measure seam durability | Mechanical tensile testing | Guarantees durability |
Fit Testing | Verify sizing and comfort | Fit trials on models | Ensures user satisfaction |
Packaging Quality | Maintain shape and presentation | Folding, tissue stuffing | Prevents damage in transit |
Eco-friendly Packaging | Use recyclable materials | Sustainable packaging choice | Supports brand image |
Ready to customize your own high-quality baseball caps?
At Kinwin, we combine advanced equipment, strict quality control, and innovative design to deliver durable, stylish, and sustainable baseball caps tailored to your brand’s unique needs. Whether you need sporty snapbacks, classic dad hats, or trendy fashion caps, our expert team can help bring your vision to life.
Contact us today for a free consultation and quote — let’s make your perfect baseball cap together!