Baseball caps are more than just a fashion staple — they symbolize culture, sport, and personal style worldwide. Behind every well-crafted cap lies a blend of precision, innovation, and quality materials. Whether you’re a beginner or a seasoned manufacturer, understanding the entire process of making a baseball cap is key to producing a durable and stylish product that stands out in the market.
In short, making a baseball cap involves selecting quality materials, using specialized tools and machines, designing accurate patterns, assembling components precisely, and maintaining strict quality control. Sustainable materials are increasingly favored to meet modern eco-friendly standards. This guide walks you through every step of the process, empowering you to create caps that balance functionality, aesthetics, and environmental responsibility.
Let me share a quick story: One of our clients once struggled to keep their baseball caps durable under harsh outdoor conditions. After refining their materials and assembly methods, their customer satisfaction soared — proving that mastering the craft behind a baseball cap can transform a product from ordinary to exceptional. Ready to dive in? Let’s start exploring.
1.What materials are needed to make a high-quality baseball cap?
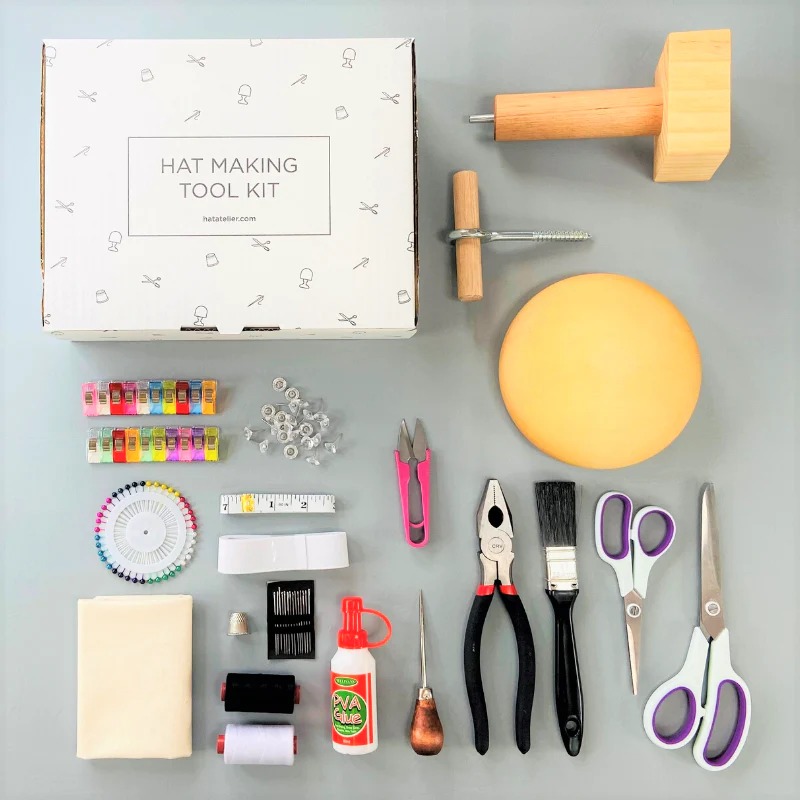
High-quality baseball caps require durable fabrics such as cotton twill, polyester blends, or wool. Other essential materials include a sturdy sweatband, a plastic or metal adjustable strap, stiff buckram for shaping the crown, and a firm visor insert.
- Fabric Types and Properties Cotton twill offers breathability and comfort, making it popular for casual caps. Polyester blends add wrinkle resistance and durability, ideal for sports caps. Wool is classic for premium caps, providing warmth and a unique texture.
- Buckram Stiffening Buckram is a stiff cotton fabric used inside the front panels to keep the cap’s shape. Different weights of buckram affect the firmness — heavier buckram creates a more structured crown.
- Sweatband Materials Typically made from cotton or synthetic blends, sweatbands improve comfort and absorb moisture. Some advanced sweatbands use antimicrobial fabrics to reduce odor.
- Visor Components Visors are reinforced with plastic or cardboard inserts. Plastic inserts are more durable and weather-resistant, while cardboard is cheaper but less water-resistant.
- Sustainable Material Trends Brands increasingly use organic cotton, recycled polyester, and biodegradable buckram alternatives to reduce environmental impact.
Material | Purpose | Typical Use Case | Sustainability Considerations |
---|---|---|---|
Cotton Twill | Fabric exterior | Casual and fashion caps | Organic cotton available |
Polyester Blend | Fabric exterior | Sports and outdoor caps | Recycled polyester options |
Wool | Fabric exterior | Premium caps | Renewable but resource-intensive |
Buckram | Crown stiffening | All structured caps | New eco-friendly buckram alternatives |
Plastic Insert | Visor reinforcement | Durable and weatherproof | Harder to recycle, but long-lasting |
Cardboard Insert | Visor reinforcement | Budget caps | Biodegradable, less durable |
Sweatband | Comfort and moisture control | All caps | Antimicrobial and recycled materials |
2.Which tools and machines are essential for baseball cap manufacturing?
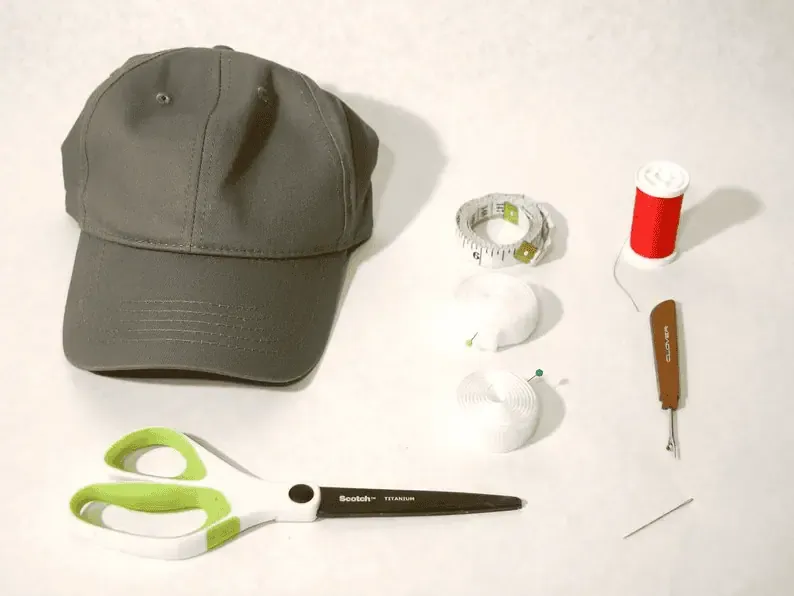
Key tools include industrial sewing machines, embroidery machines, pattern cutters, heat press machines, and specialized pressing tools to shape the cap.
- Industrial Sewing Machines These handle high-volume, precise stitching for seams, visors, and sweatbands. Different machines may be specialized for straight stitching, overlocking, or zigzag patterns.
- Embroidery Machines Modern caps often feature embroidered logos or designs. Computerized embroidery machines enable complex patterns with speed and consistency.
- Pattern Cutting Machines Automated cutters improve fabric utilization and ensure precise shapes for cap panels.
- Heat Press Machines Used for attaching patches, decals, or sublimation prints on caps.
- Pressing Tools and Hats Forms Specialized molds help shape the crown and visor during pressing, ensuring uniformity.
- Manual Tools Scissors, awls, needles, and pins remain essential for detailed finishing and adjustments.
- Emerging Technologies Laser cutting and 3D printing for prototype parts are gaining traction in innovative cap production. Tool/Machine Purpose Notes Industrial Sewing Machines High-volume, precise stitching for seams, visors, sweatbands Specialized for straight, overlock, zigzag stitching Embroidery Machines Creating embroidered logos and designs Computerized for complex patterns and speed Pattern Cutting Machines Automated cutting for precise fabric panel shapes Improves fabric utilization Heat Press Machines Attaching patches, decals, sublimation prints For surface decoration Pressing Tools & Hat Forms Shaping crown and visor during pressing Ensures uniformity Manual Tools Scissors, awls, needles, pins for finishing Essential for detailed adjustments Emerging Technologies Laser cutting, 3D printing for prototypes Innovative manufacturing methods
Tool/Machine | Purpose | Notes |
---|---|---|
Industrial Sewing Machines | High-volume, precise stitching for seams, visors, sweatbands | Specialized for straight, overlock, zigzag stitching |
Embroidery Machines | Creating embroidered logos and designs | Computerized for complex patterns and speed |
Pattern Cutting Machines | Automated cutting for precise fabric panel shapes | Improves fabric utilization |
Heat Press Machines | Attaching patches, decals, sublimation prints | For surface decoration |
Pressing Tools & Hat Forms | Shaping crown and visor during pressing | Ensures uniformity |
Manual Tools | Scissors, awls, needles, pins for finishing | Essential for detailed adjustments |
Emerging Technologies | Laser cutting, 3D printing for prototypes | Innovative manufacturing methods |
3.How is the pattern and design created for a baseball cap?
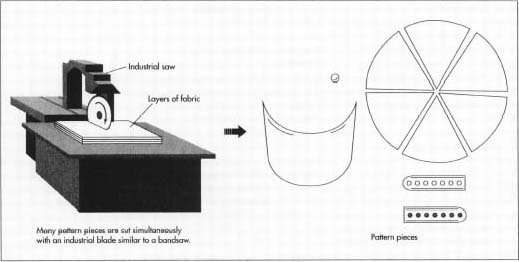
Patterns are first drafted based on cap style, then refined through sampling. Digital design software helps create accurate patterns that ensure perfect fitting panels and components.
- Initial Concept and Sketching Designers begin with sketches focusing on style, panel number (usually six or five), visor shape, and closure type.
- Pattern Drafting Using traditional paper or CAD software, patterns for each panel, visor, sweatband, and lining are created.
- Sample Production and Fitting Prototypes are sewn to test fit and structure. Adjustments are made to correct size, panel curvature, and comfort.
- Digital Tools for Precision Software like AutoCAD or Adobe Illustrator streamline the design-to-production workflow.
- Customization Options Patterns can be adapted for embroidery placement, fabric choices, and special trims like piping or eyelets.
- Sustainability in Design Designing with fabric yield optimization reduces waste and supports eco-friendly production. Step Description Notes Initial Concept and Sketching Designers create sketches focusing on style, panel count, visor shape, and closure type Usually 5 or 6 panels Pattern Drafting Patterns for panels, visor, sweatband, and lining created using paper or CAD software Traditional or digital methods Sample Production and Fitting Prototypes sewn to test fit, structure, and comfort; adjustments made as needed Ensures accurate size and panel curvature Digital Tools for Precision Software like AutoCAD, Adobe Illustrator used to streamline design-to-production workflow Enhances accuracy and efficiency Customization Options Patterns adapted for embroidery placement, fabric choices, trims like piping or eyelets Allows personalized designs Sustainability in Design Fabric yield optimization during pattern making to reduce waste and promote eco-friendly production Supports sustainable manufacturing
Step | Description | Notes |
---|---|---|
Initial Concept and Sketching | Designers create sketches focusing on style, panel count, visor shape, and closure type | Usually 5 or 6 panels |
Pattern Drafting | Patterns for panels, visor, sweatband, and lining created using paper or CAD software | Traditional or digital methods |
Sample Production and Fitting | Prototypes sewn to test fit, structure, and comfort; adjustments made as needed | Ensures accurate size and panel curvature |
Digital Tools for Precision | Software like AutoCAD, Adobe Illustrator used to streamline design-to-production workflow | Enhances accuracy and efficiency |
Customization Options | Patterns adapted for embroidery placement, fabric choices, trims like piping or eyelets | Allows personalized designs |
Sustainability in Design | Fabric yield optimization during pattern making to reduce waste and promote eco-friendly production | Supports sustainable manufacturing |
4.What are the key steps involved in assembling a baseball cap?
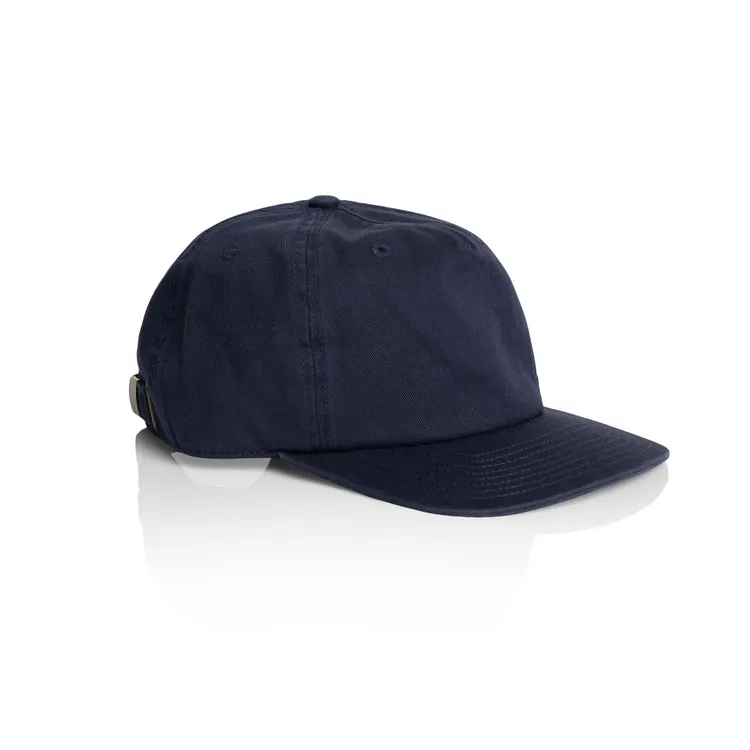
Assembly typically follows these steps: cutting fabric, stitching panels, attaching buckram, sewing the visor, adding sweatband, closing the crown, and installing closure mechanisms.
- Cutting Fabric Panels Using patterns, fabric pieces for each panel, visor, sweatband, and lining are cut precisely.
- Applying Buckram to Front Panels Buckram is fused or sewn to front panels to maintain shape.
- Sewing Panels Together Panels are sewn edge-to-edge, forming the cap crown.
- Constructing the Visor Fabric is wrapped and sewn over the visor insert.
- Adding Eyelets and Ventilation Eyelets can be stitched or metal grommets added for breathability.
- Attaching Sweatband Sweatband is sewn inside for comfort and moisture absorption.
- Closing the Crown The top button is attached, and final seams closed.
- Installing Adjustable Closure Snapback, strapback, or fitted closures are fixed at the rear.
- Quality Inspection Finished caps undergo inspection for stitching consistency, fit, and defects.
Step Number | Process | Purpose | Key Quality Factors |
---|---|---|---|
1 | Cutting fabric | Accurate panel shaping | Precision and fabric layout |
2 | Attaching buckram | Crown firmness | Proper adhesion and weight |
3 | Stitching panels | Forming cap shape | Seam strength and alignment |
4 | Constructing visor | Stiffening and shaping visor | Even stitching and contour |
5 | Adding eyelets | Breathability | Secure and symmetrical |
6 | Sewing sweatband | Comfort and moisture control | Softness and durability |
7 | Closing crown | Final cap form | Seam neatness |
8 | Installing closure | Adjustable fit | Secure and functional |
9 | Quality inspection | Product consistency | Defect-free final product |
5.How do you ensure quality control and durability in baseball caps?
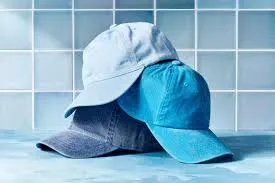
Quality control includes checking material consistency, stitch strength, colorfastness, shape retention, and hardware durability.
- Material Testing Verifying fabric tensile strength, shrinkage rate, and colorfastness under UV exposure.
- Stitch Inspection Counting stitches per inch (usually 8-10 SPI for durability) and testing seam pull strength.
- Shape and Fit Evaluation Using standardized hat blocks to ensure caps keep shape after multiple wears.
- Hardware Durability Testing snapbacks and strap closures for repeated use cycles.
- Environmental and Wear Testing Caps are subjected to sweat simulation, washing, and abrasion tests.
- Continuous Improvement Customer feedback loops and production audits drive quality enhancements. Quality Control Aspect Description Key Points Material Testing Verify fabric tensile strength, shrinkage, and colorfastness under UV exposure Ensures fabric durability and color retention Stitch Inspection Count stitches per inch (8-10 SPI) and test seam pull strength Confirms seam durability Shape and Fit Evaluation Use standardized hat blocks to check shape retention after wear Ensures consistent fit and form Hardware Durability Test snapbacks and strap closures for repeated use cycles Validates closure mechanism longevity Environmental and Wear Testing Subject caps to sweat simulation, washing, and abrasion tests Assesses performance under real-life conditions Continuous Improvement Use customer feedback and production audits to enhance quality Drives ongoing product refinement
Quality Control Aspect | Description | Key Points |
---|---|---|
Material Testing | Verify fabric tensile strength, shrinkage, and colorfastness under UV exposure | Ensures fabric durability and color retention |
Stitch Inspection | Count stitches per inch (8-10 SPI) and test seam pull strength | Confirms seam durability |
Shape and Fit Evaluation | Use standardized hat blocks to check shape retention after wear | Ensures consistent fit and form |
Hardware Durability | Test snapbacks and strap closures for repeated use cycles | Validates closure mechanism longevity |
Environmental and Wear Testing | Subject caps to sweat simulation, washing, and abrasion tests | Assesses performance under real-life conditions |
Continuous Improvement | Use customer feedback and production audits to enhance quality | Drives ongoing product refinement |
6.Are sustainable and eco-friendly materials used in modern baseball cap production?
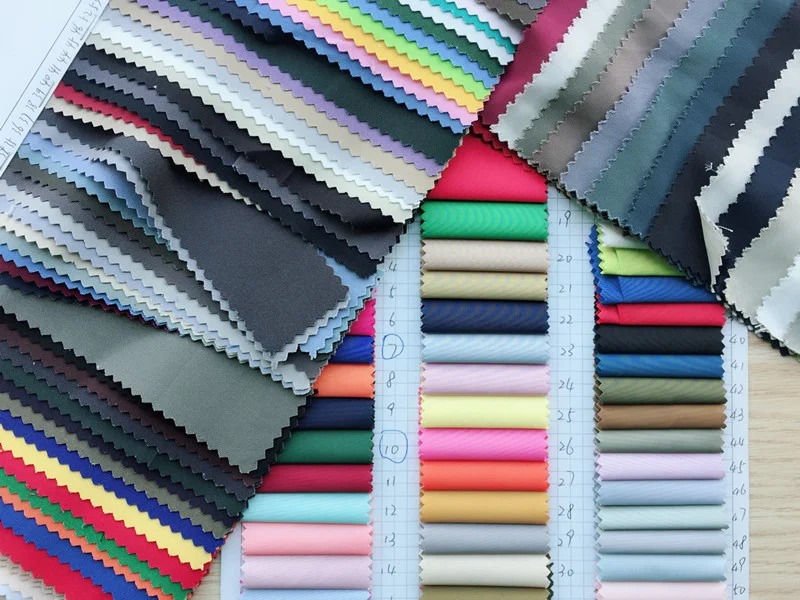
Yes, the industry increasingly adopts organic cotton, recycled polyester, biodegradable buckram, and eco-friendly dyes to reduce environmental footprint.
- Organic and Recycled Fabrics Organic cotton avoids harmful pesticides. Recycled polyester reduces plastic waste.
- Innovative Buckram Alternatives Biodegradable or plant-based buckram materials are emerging.
- Eco-Friendly Dyeing Processes Low-water, non-toxic dyeing methods minimize pollution.
- Supply Chain Transparency Certifications like GOTS (Global Organic Textile Standard) and OEKO-TEX ensure responsible sourcing.
- Trade-Offs and Costs Sustainable materials often cost more, and balancing price with eco-values remains a challenge.
- Consumer Demand Increasing demand for green products motivates brands to invest in sustainability. Sustainability Aspect Description Key Points Organic and Recycled Fabrics Organic cotton avoids pesticides; recycled polyester reduces plastic waste Promotes safer farming and plastic reduction Innovative Buckram Alternatives Emerging biodegradable or plant-based buckram materials Eco-friendly alternatives to traditional buckram Eco-Friendly Dyeing Processes Low-water, non-toxic dyeing methods to minimize pollution Reduces environmental impact Supply Chain Transparency Certifications like GOTS and OEKO-TEX ensure responsible sourcing Guarantees eco-friendly and ethical practices Trade-Offs and Costs Sustainable materials usually cost more; balancing price and values is challenging A key consideration for manufacturers and brands Consumer Demand Growing consumer interest drives brands to adopt sustainable practices Market-driven push for greener products
Sustainability Aspect | Description | Key Points |
---|---|---|
Organic and Recycled Fabrics | Organic cotton avoids pesticides; recycled polyester reduces plastic waste | Promotes safer farming and plastic reduction |
Innovative Buckram Alternatives | Emerging biodegradable or plant-based buckram materials | Eco-friendly alternatives to traditional buckram |
Eco-Friendly Dyeing Processes | Low-water, non-toxic dyeing methods to minimize pollution | Reduces environmental impact |
Supply Chain Transparency | Certifications like GOTS and OEKO-TEX ensure responsible sourcing | Guarantees eco-friendly and ethical practices |
Trade-Offs and Costs | Sustainable materials usually cost more; balancing price and values is challenging | A key consideration for manufacturers and brands |
Consumer Demand | Growing consumer interest drives brands to adopt sustainable practices | Market-driven push for greener products |
Ready to Customize Your Baseball Caps with Kinwin?
At Kinwin, we combine cutting-edge manufacturing technology with sustainable practices to bring your baseball cap ideas to life. Whether you want classic designs or trendy customizations, our expert team ensures every cap meets the highest standards of quality and environmental responsibility.
Contact us today to request a quote and start your custom baseball cap journey! Email: [[email protected]] | Website: [https://plushtoyinchina.com]